Extracting Broken Bolts Using an Extractor
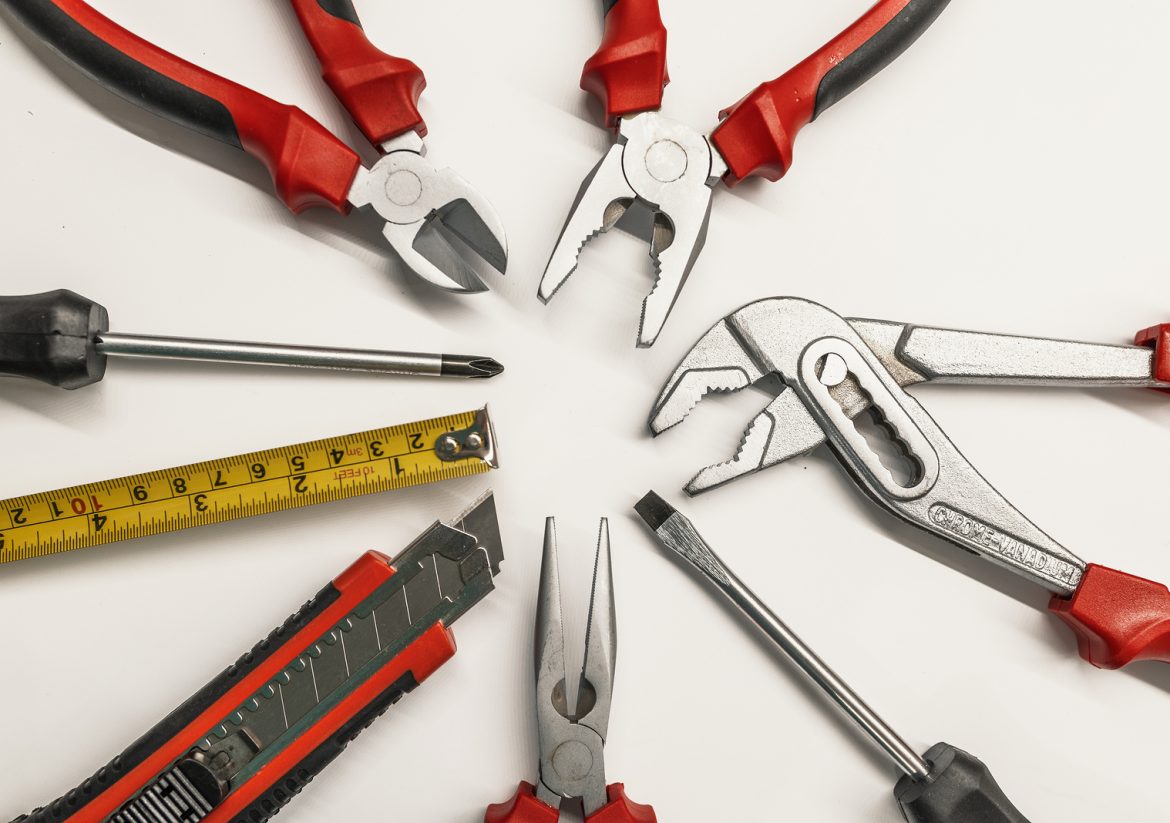
Extracting Broken Bolts Using an Extractor
Today I’m going to explain how to extract a broken fastener without damaging threads.
I have an assortment of hex type extractors, T handle type extractors, and left handed drill bits. A left hand drill bit is different from a conventional right hand bit because it only cuts if the drill’s rotating in a counterclockwise direction. The reason I prefer left handed bits to right handed bits is, let’s say you’re drilling out a fastener, it goes into a blind hole. That means that there’s no exit point for the fasteners. You’re drilling with your right handed bit, the bit grabs the fastener, drives it further down and tighter into that hole, that’s going to make it that much more difficult for you to extract that fastener. If it’s not a blind hole, in other words the holes open on the other side, a right hand bit can drive the fastener out of its hole and drop it into this void where you don’t want it. For example, into a coolant passage if you’re trying to extract a water pump bolt. Let’s say you’re using a left handed bit. These bits cut while turning in a counterclockwise direction, and it backs the fastener out, and you may not even need to use an extractor in the first place. So if you can, use left handed bits.
First let’s examine T handle type extractors, since they’re what’s widely available at most auto parts stores. On T handle type extractors you’ll see that they recommend a drill bit size to use. For example use a 7/64th drill bit. If you don’t have the exact size drill bit you can always go a size up because the extractors are tapered, so going a size up won’t be a problem. The next size up from 7/64th would be 1/8”.
I’m not going to use the T handle type extractors. I’m using the hex type reverse thread tapered spiral extractors. I’ve determined that 1/8” bit is the proper size to drill for a particular size fastener, and it’ll give me a bit of room around the edges so I don’t accidentally drill out the threads. You have to think, you may not be perfectly on center, you may be a little bit crooked, and if you are, are you going to go into the threads, because if you mess up the threads, then you’ll have to drill them out, and either Hela coil it or tap to a larger size, and use a different size fastener. That’s what you’re trying to avoid by using an extractor set in first place, so just be careful.
Hela coiling is a process where you drill out the old fastener in the threads with a bit larger than the original fastener diameter. You then tap it using a special Hela coil tap. The special tap allows you to thread a spiral insert into the hole. This insert allows you to use the original sized fastener in the larger tapped hole. So to verify that it’s the proper diameter just take the fastener, place the opposite end of the bit right over it, and you’ll be able to see if it’s too large or too small.
Be very careful when selecting your bit size. If the holes too small you have a higher likelihood of snapping the extractor off in the fastener. A smaller extractor can’t handle as much torque as a larger one, while a hole that’s too large may damage the threads. So you want the hole to be not too large, and not too small. Now if you’re using a T handle type extractor you use the 7/64 marked extractor we discussed earlier.
Let’s look at a fastener that got sheared off. The first thing I’m gonna do is center punch it. You want to make sure you get as close to the center as possible. Use the left handed bit; get it on that center punched hole. You want to drill as straight as possible to avoid damaging the threads. It’s especially important to maintain the proper angle as you begin drilling, because the bit will tend to maintain that angle after the hole is started. When you begin to drill, start slow to prevent the bit from walking out of the punched hole. Pulse the drill on and off when starting the hole to achieve the same result. Make sure you’re using a sharp bit. A sharp bit will produce metal filings whereas a dull bit will force you to press harder, which will increase the likelihood of snapping off the bit, or worse snapping it off the fastener. It’s also not a bad idea to spray some penetrating oil on the fastener before removing it. To get the extractor to bite in there better, pop it in there, and give it a few taps with a hammer. Spiral broken screw extractors are made by several companies such as Irwin, Klein, Stanley, Craftsman, and Tech Team https://techteamproducts.com/. I like the Tech Team’s https://www.amazon.com/Broken-Extractor-Remove-Damaged-Screws/dp/B07CV2ZR59/ref=sr_1_233?ie=UTF8&qid=1546980813&sr=8-233&keywords=broken+screw+extractor+set because of its proven quality and great instructions.
It’s important to not break off the extractor in the fastener. They’re made of hardened steel and standard high speed steel drill bits can’t drill through them. If you were to break one off you need a carbide tipped or cobalt drill bit and apply constant lubrication on the bit throughout the process and it will be a slow process. When turning the extractor, be mindful of how much twisting. A bit of twist is fine, but too much and it can snap. If you feel that the extractor is about to break, remove it and hit the fastener with more penetrating oil, wait for it to penetrate, and try again. If that doesn’t work you’ll have to drill out the fastener and the threads, and either retype the hole to a larger size or Hela coil it.
Put the ½” socket on there, turn it counterclockwise, and the fasteners already coming out. There it is. Now just pop a new bolt in. To release the fastener from the extractor, tightly grab it with a pair of vice grips, and then just twist the extractor clockwise. It only bites in when it’s going counterclockwise.