Oxygen and Acetylene Cutting Everything You Need to Know
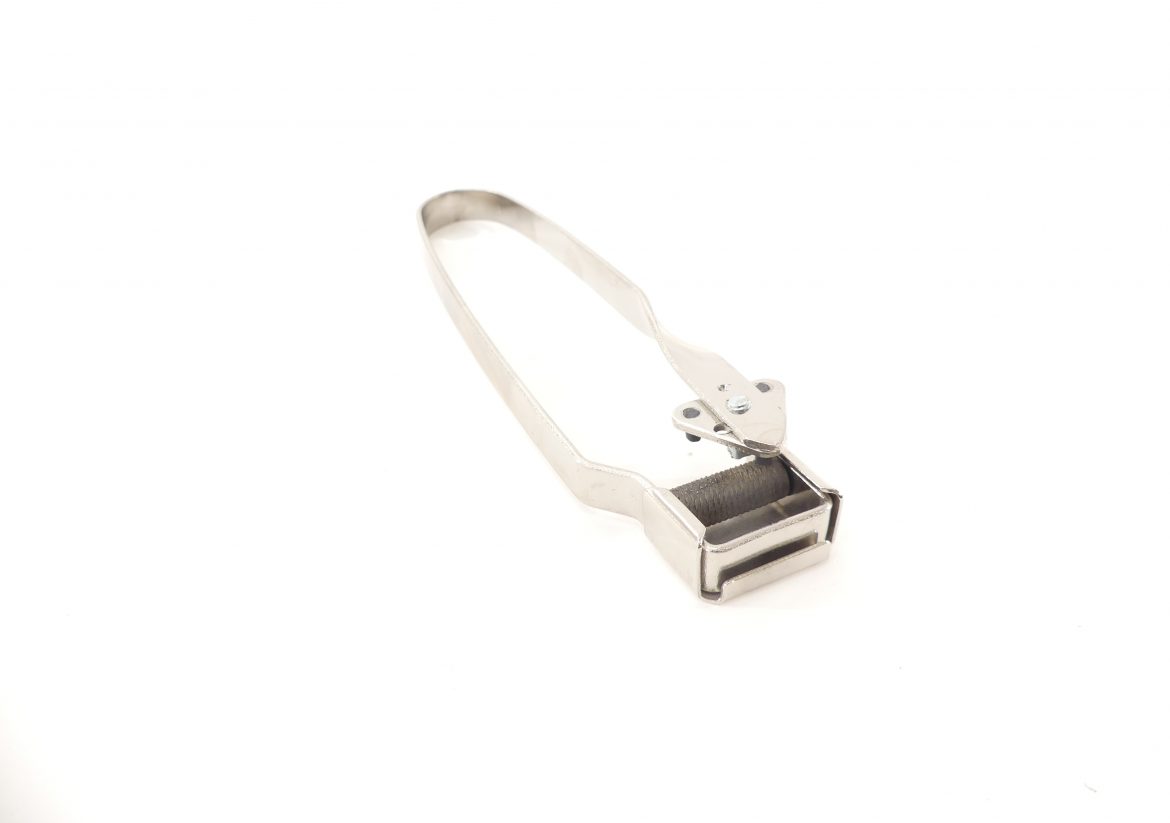
Oxygen and Acetylene Cutting Everything You Need to Know
I’m going to explain oxy fuel systems and the process of oxy fuel cutting, I say oxy fuel because gases other than acetylene like propane can be used. But we’re discussing the highly flammable acetylene gas combined with pure oxygen. I have a typical portable oxy fuel rig that you would find in any shop or garage. In fact, no shop or garage would be complete without this setup. It has many uses beyond simply cutting steel, for example, fitting parts for forming, pre heating and post heating during certain welding procedures, and scarfing, which is the removal of excess material by burning it away, and also oxy fuel welding which predates ARC welding and is still used in some places where ARC welding is not an option. Oxy fuel also has implications in hard facing and surfacing for the repair and strengthening of worn or wearing parts.
Now let’s move on to the equipment. We have an acetylene tank or cylinder that it is shorter than the green oxygen cylinder. Inside the cylinder is a porous material which has been soaked in acetone. This will absorb acetylene unless the pressure inside the cylinder goes beyond 15 PSI, a point at which acetylene becomes dangerously unstable. To find out just how dangerous this can be do a Hey Siri or Hey Alexa search for acetylene cylinder accidents. The wider cylinder provides more area for the acetylene to remain separated from the other materials. Thus, it is never a good idea to lay an acetylene cylinder on its side. This will result in the mixture of the different materials and the dilution of the acetylene gas. You should allow at least 12 hours in an upright position in the event that the cylinder should lay on its side for any length of time. The oxygen cylinder is simply filled with compressed gas and does not require such special handling. However, the oxygen is under tremendous pressure and will become a deadly projectile should it become punctured or if the tank valve breaks off. These tanks are spun from a single piece of steel rather than seam welded like a piece of pipe, and they are routinely inspected and discarded once they have been compromised. Moving onto the valves and gas regulators, the oxygen cylinder valve is factory installed and should never be tampered with due to the immense pressure and risk of explosion. They are equipped with a pressure relief valve should the tank pressure exceed safe levels.
The gage set up is called a regulator. It serves two primary functions. It tells us the current gas pressure inside the cylinder, which gives us an indication of the amount of gas left and it also regulates the working pressure to the torch for oxy fuel. We measure this in pounds per square inch or PSI. This is different from the flow of shielding gas for ARC welding, which is measured in cubic feet per hour or CFH. The working pressure is adjusted using the adjusting screw. Acetylene cylinders have similar valves and regulators however, there are differences. The cylinder valve does not have a pressure relief valve. These are located on the bottom of the cylinder and the valve itself is different from the oxygen cylinder valve. The regulator is essentially the same with the exception of the gauges which are calibrated for low pressures.
Let’s talk about the other end of the operation. There is the torch body, the one we have is the Victor J series torch, which is their smallest torch. Most shops and contractors will have the journeyman model, which is a larger version, but it works the same. The torch body is essentially a mixing chamber for the two gases which are supplied by the gas hoses. The hoses are color coded as well as have opposite threads, green hose and right handed threads for oxygen and red hose with left handed threads for the fuel line. I have equipped my set with optional, yet highly recommended, check valves to prevent the flow of gas from returning to the cylinder. Each gas line has a needle valve which turns the gas on and off at the torch, so there is no need to be close to the cylinder while working. This also allows for flame adjustments. The torch has a threaded end for the attachment of various tips. You can use a welding tip which can also be used for heating. A Forney medium duty or a number 4 Victor welding tip and cutting torch is a handy set up. The needle valve is used to adjust the oxygen pressure to the tip of the pre heating flame. It also has a lever valve which activates the full oxygen pressure for cutting. The cutting tips are removable and come in a range of sizes. There are many holes in the tip. The outer holes are the pre heating holes, the center hole is the cutting hole, it is a larger diameter orifice. Periodically this hole can become clogged with slag and need to be cleaned out. A tip cleaner set is used to clean the holes and file the tip to a clean condition when setting up the torch. Remember keep your tip clean, get comfortable before you start, and concentrate on the cut while it’s happening. To get some good tip cleaning tips do a Hey Google search for correct acetylene torch tip cleaning process. Good brands of tip cleaners include Victor, Irwin, US Forge, and Tech Team https://techteamproducts.com/. We like Tech Team’s 762 Tip Cleaner Set because it has all the correct size reamers, a file, and it comes in a handy storage case. https://www.amazon.com/Tech-Team-Long-Pattern-Cleaner-Oxy-Acetylene/dp/B07NGV9CS2/ref=sr_1_1?keywords=tech+team+tip+cleaner&qid=1553187220&s=gateway&sr=8-1
It is good practice to position the torch body needle valves away from your arm or towards the ground. This prevents them from being disturbed while cutting and welding otherwise, your sleeves and gloves can rub against them and change the settings. When you’re ready to open the cylinders and set the regulators and torch for cutting, you should always stand off to the side of the regulator while cracking the valves. Should the valve or gauges have a failure debris could be blown out towards the front of the gauges, so it is best to be clear of them.
Always open valves slowly to prevent damage to the regulator. There is a tremendous amount of pressure being released and these regulators are sensitive. Open the oxygen cylinder valve all the way and be sure to seat the valve in the open position. This is a double sided valve, which means that it only seals when fully open or closed. Otherwise there is potential for leakage. Now use the adjusting screw to set the working pressure to 40 PSI. This is a standard pressure for cutting. Now open the acetylene cylinder valve in the same manner as the oxygen valve, except only open the valve slightly. No more than one full turn. This way the fuel valve can be shut off quickly in an emergency. This valve will not leak under these circumstances. Next set the working pressure to just above 5 PSI. The actual working pressure needed is 5 PSI but will be reduced when the torch needle valve is opened, we compensate for this by setting it slightly higher. This generally is not a problem with a higher pressure oxygen line. So no need to worry there. Next, it’s time to set up the torch. First open the oxygen needle valve on the torch body all the way. This is our cutting pressure, so we need the full 40 PSI set at the regulator. The next two needle valves are only open when we are ready to ignite the flame and start cutting.
We need an ignition source for this, so we use a striker. Before we attempt acetylene ignition, we need to verify that our striker is working, so we give it a few pumps so we are confident that we can quickly ignite the gas. The safest and best way to light your oxy acetylene torch is to use a flint striker. Basically, this is a device that has a flint member that is fixed into a threaded socket that screws into a spring loaded member that moves back and forth against a hardened steel surface like a file. This assembly is held inside a protective steel cap about 1” in diameter x ½” deep. When the striker is activated by hand pressure, the flint moves across the steel file and creates sparks. These sparks, of course, will ignite the acetylene, and the steel cap will keep the flame from unexpectedly projecting too far. These strikers are made by many companies such as: Forney, Hobart, Ally Tools, Vas Tools, Hot Max, US Forge, Lincoln Electric, Worthington, Levado, and Tech Team https://techteamproducts.com/. Tech Team’s model 763 Flint Striker https://www.amazon.com/Lighter-Igniter-Oxy-Acetylene-Tech-Team/dp/B07NGS8PLY/ref=sr_1_33?crid=2QQKZ0LGHZBCF&keywords=flint+striker+welding&qid=1565098867&s=gateway&sprefix=flint+striker+welding%2Caps%2C124&sr=8-33 is the one we like the best because it has high quality construction with a durable zinc plating, and it contains 3 flints that can easily be rotated one to the next to the next as it wears down and becomes ineffective. It probably also occurs to you that eventually these flints will wear out and oddly enough there are several companies that make replacement flints such as: Forney, US Forge, Shurlite, Zippo, and Tech Team https://techteamproducts.com/. We happen to like Tech Team’s item 761 https://www.amazon.com/Replacement-Strikers-Oxy-Acetylene-Tech-Team/dp/B07NGNFK2V/ref=sr_1_1?keywords=tech+team+flint&qid=1565108056&s=gateway&sr=8-1which contains 3 sets, each set having 3 replacement flints, which easily fits into their 763 3 Flint Striker. We slightly open the gas needle valve on the torch and quickly engage the striker directly at the cutting tip. We should have ignition. Now you’ll notice a yellow flame with a lot of black soot pouring off of the end. This is unburned gas, which means we need to turn up the heat by increasing our feed and slowly open the gas needle valve and you will see the flame leave the tip of the torch. Then back it off just enough to bring the flame in contact with the tip. Next, slowly open the oxygen needle valve on the cutting torch. You should now have a blue flame. Continue opening the valve until you reach what is called a neutral flame. You will see a small blue cone inside the outer flame when the cone reduces down to smaller blue heating cones you’ve achieved in neutral flame. This is reaching extremely high temperatures, so it is very important to be aware of what you’re pointing the torch at before we get to cutting.
We also need to know how to properly shut down the system. First, we shut off the acetylene needle valve on the torch, then close the oxygen needle valve. Next, closed both cylinder valves. Then squeeze the oxygen lever until the gauges on the regulator show zero pressure. Now open the gas needle valve on the torch to bleed the fuel line being sure the two gauges show zero PSI. Close the gas needle valve and the oxygen needle valve on the torch. Now back off the adjusting screw on both regulators until they are loose. Being careful not to remove them.
You are now ready to begin cutting. Most cutting applications will be done on various thicknesses of steel plate and sheet. Cuts can be straight or curved. The same principles will be applied to curved cuts. For most cuts you will likely be following marks such as lines drawn by soapstone. These can withstand high temperatures and can be seen during the cutting process. Frequently when you are using a torch to cut metal, you need to mark where you are going to cut. There are lots of ways to make a mark or a line that range from using a magic marker or sharpie, or just scratching the metal with an awl. The best way to make the marks you need is to use soapstone, which is the solid form of the same talc that is used in talcum powder. The handiest way to do this is to use pre-cut rectangular (127 x 12.7 x 4.8mm) prismatic pieces of talc, which are held in a special pen shaped device with a pocket clip that allows the talc to be firmly held and advanced as the talc wears down. These soap stone holders are available from many companies such as: Forney, Ally Tools, Hobart, Firepower, and Tech Team® https://techteamproducts.com/. We happen to like Tech Team’s model 759 the best https://www.amazon.com/Soapstone-Retractable-Oxy-Acetylene-Tech-Team/dp/B07NGJ4MB1/ref=sr_1_3?keywords=tech+soapstone+holder&qid=1565098360&s=gateway&sr=8-3 because it has a durable zinc finish and a positive locking and advancing mechanism for the soap stone.
Of course, you also need soap stone refills, aka talc, to feed the holder as you wear out the soap stone. Those refills are available from several companies such as: Homee, Anchor, VasTools, Uniweld, Hobart, and also Tech Team® https://techteamproducts.com/. We like Tech Team’s 757 36 pc. of soap stone https://www.amazon.com/Tech-Team-Soapstone-Machining-Surfaces/dp/B07JMFBFW3/ref=sr_1_44?crid=13B5M9FVHOOXU&keywords=soap+stone+holder+welding&qid=1565097627&s=gateway&sprefix=soap+stone%2Caps%2C128&sr=8-44 the best because it is high quality, bright white soap stone that leaves clear and easy to erase marks on almost any metal surface. In order to follow your lines you need to be properly supported and be able to comfortably move the torch along the line without stopping. It is best to start your cut on the edge of the plate and move smoothly across the cut at a steady pace to initiate the cut. Hold the heating tips halfway over the edge until you see the metal reach a light orange color. At this point, the steel has reached its kindling temperature and will burn away when a high pressure oxygen stream is introduced. Now fully depress the lever valve to start the cutting process. There is a chemical oxidation reaction between the heated iron and the oxygen. This process can be used to cut through steel up to 10 inches thick. A small Victor or Harris torch is nearly capable of cutting through a two inch thick axle.
Lean against your welding table and prop the torch with your arm as this will create a very stable condition for cutting. Verify that you can comfortably maneuver the torch along the entire cut before you begin. The perfect cut will be smooth clean looking and will leave little or no slag underneath. This means the operator held the torch at the proper angle, typically 90 degrees and used a proper consistent speed. If you move too fast, you will lose your cut or not achieve complete penetration, and a slow cut will leave a washed out lock with a lot of slag underneath. The more you practice, the better your cutting will be. Most welding students don’t spend enough time at the cutting table. People who cut on a regular basis can achieve cuts that look robotic. It’s all about practice. Now let’s take a look at the technique of piercing. This is used to cut holes in plate when you can’t start from the edge. These holes generally need to be perpendicular to the surface of the plate. So holding the torch at 90 degrees is critical. This creates an issue at the start of the preheat however, if we begin the preheat at 90 degrees, the burned material needs somewhere to go and will end up blowing right back into the tip. To get around this, we always start our piercings with the torch at a slight angle. This forces the material to blow out to the side. Once full penetration is achieved, move the torch back to a 90 degree condition and make the cut. It is best to start at the part of the material that will be lost in the process, then move the cut to the marks.