I needed to make a repair on my irrigation system and it was necessary to use a clamp on the tubing.
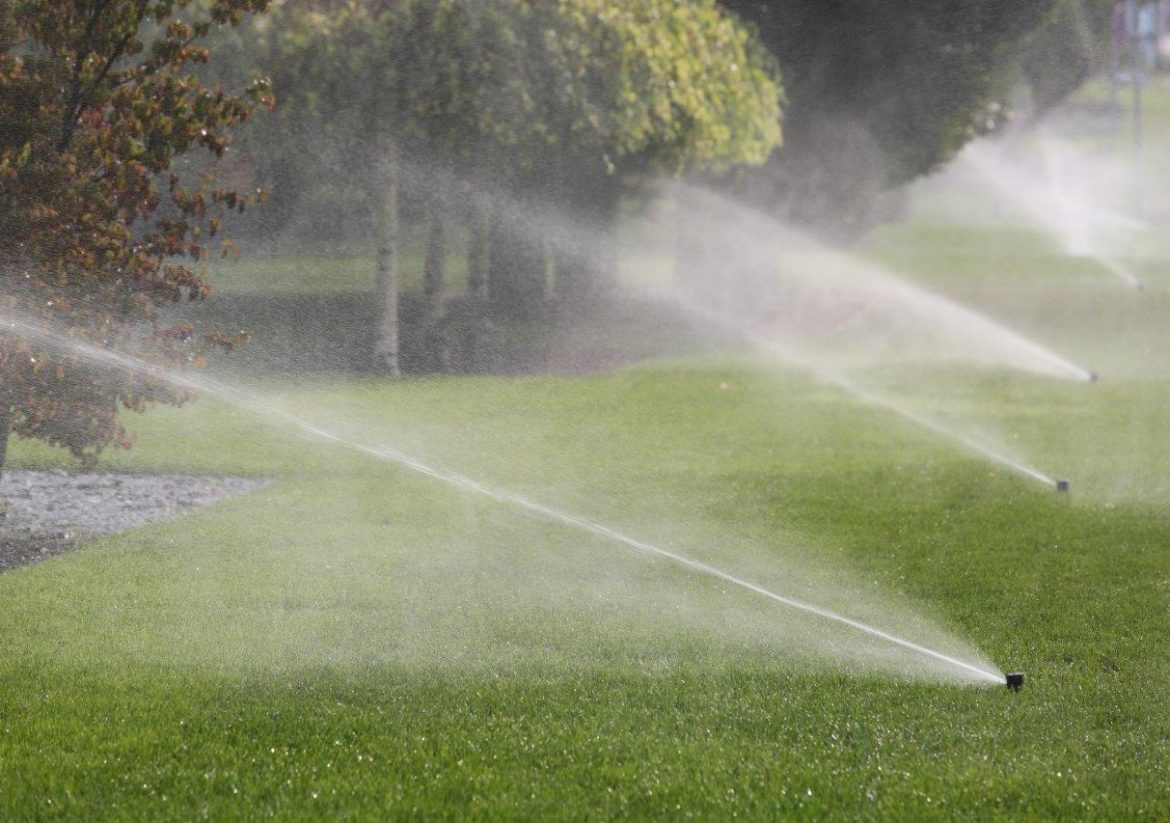
I needed to make a repair on my irrigation system and it was necessary to use a clamp on the tubing.
You would think that clamping a hose or a fitting would be a simple straight forward project, but when I got online I discovered that there is an unbelievable array of clamps and each one tends to be best for a specific application. Before you go out and buy a clamp check this out:
There are band clamps. These have a smooth uniform interior surface. Generally speaking they are tightened by using a special tool that crimps them. One of the common uses of this type of clamp is for PEX plumbing applications where the PEX tubing must be very firmly and securely attached to a barbed brass fitting. These clamps are almost always made of some type of steel that provide uniform pressure around the entire perimeter of the tube. The crimping tool is a substantial affair with vinyl padded grips that require significant pressure to make the clamp tight. To remove one of these clamps, the clamp must be destroyed as it is not reusable.
There are ear clamps which are made from heat treated/tempered steel wire. Generally speaking, it is two pieces of wire that form a loop, and one piece goes inside the other and on the ends there are ears. This type of clamp provides uniform pressure around its perimeter and is, generally speaking, for low pressure applications such as fuel lines on lawn mowers, as it can easily be opened and closed by pinching the ears together either with pliers, or if the ears are big enough, by simple hand pressure. These clamps are size specific and require that the inside diameter of the clamp is very closely matched to the outside diameter of the tubing.
There are ratchet clamps which are almost always made from plastic and generally speaking can be tightened with simple hand pressure. As the name implies, the clamp has a small internal ratcheting mechanism that engages as it is compressed. These are for low pressure applications, but they can be released and are reusable. The inside diameter of the clamp must closely match the outside diameter of the tube that it is securing.
There are spring hose clamps. This clamp can provide substantial pressure and therefore can be used on higher pressure applications. It is similar in construction to the ear clamp in that it is made from tempered/heat treated steel wire, but rather than using pressure to pull the ears together and open the clamp, this clamp uses a nut and screw through the two ears, and when the screw is tightened the clamp is compressed and applies pressure to the tubing. The clamp provides uniform pressure and obviously as the diameter of the wire is increased, the ability to increase the tightening pressure also increases. These clamps are size specific and the inside dimension of the clamp must also closely match the outside dimension of the tube otherwise they will not fit properly. They are commonly used on an automobile’s heater hoses.
There are T bolt clamps. These clamps can provide very high tension, and are used in applications where there is high pressure and dependability is of paramount importance. One of the applications where you see this clamp is on the high pressure hose on automotive turbo charging systems. The clamp is, generally speaking, between 1”-2” wide. It is constructed from spring steel and has a T shaped bolt mechanism for tightening. The bolt can generally be tightened by either a Phillips head screw driver or a socket wrench. It is a very dependable and strong clamp and is diameter specific.
There are worm drive clamps. These work on a gear principle where a screw that typically has a 5/16” hex head and a Phillips slot in the top of it turns a spiral screw (gear) that engages progressive slots in a stainless steel band. This is one of the most common types of clamps, and as I found out, this is the most appropriate one to use for my irrigation system. In this case, not only is the clamp reusable, but one size clamp can fit a fairly wide range of tubing sizes. For instance, a clamp that is designed to fit 1 ¼”ID tubing can also be successfully used on 1” ID tubing. To use this clamp simply slide it over the tube, slide the tubing over the fitting, and then use a Phillips head screw driver or 5/16” socket wrench to tighten the clamp to the point where there is no leakage. These clamps are commonly made with a band width of either ½” or 9/16”. Clearly the 9/16” is the strongest and this is the one I used to repair my irrigation system.
Now you have a complete education in clamps. With this knowledge you can purchase the appropriate clamp for the appropriate application. Using the wrong clamp can result in unintended consequences, such as the tubing disengaging itself from the fitting and causing all kinds of problems. Hopefully you can now avoid this type of situation.